Imagine being stranded far away with your EV's battery low. A portable charger can help you keep driving safely. As more people use EVs, these chargers are very useful. Experts say by 2025, 15% of US cars will be electric. Reliable chargers will be important for emergencies and travel. Portable EV chargers make trips easier and reduce worries on the road.
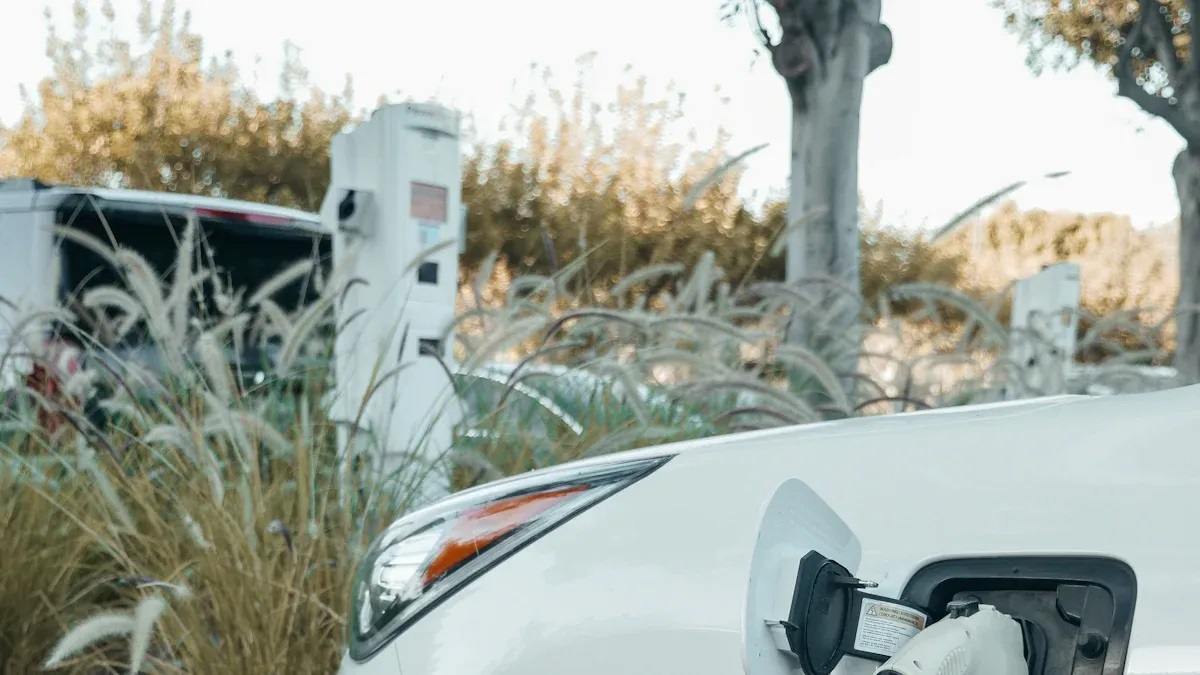
Key Takeaways
- Portable electric car charger are important for trips and emergencies. They help you keep driving without worrying about the battery.
- Pick chargers that charge quickly and work with many EV models. This will make your trips easier and more enjoyable.
- Get a charger that is light and strong. It should handle bad weather and work well while traveling.
Key Features to Look for in a Portable EV Charger
Charging Speed and Efficiency
Fast charging is important when you're traveling. Waiting too long can be frustrating. Many chargers today offer quicker speeds, like Level 2 chargers. A study shows slow charging lowers customer happiness by 141 points. Chargers with speeds around 200 kW can add lots of miles fast. This is very helpful for long trips or emergencies.
Compatibility with Different EV Models
Not all EVs use the same charging ports. Always check if the charger fits your car. Some chargers work with both NEMA 6–20 (220V/240V) and NEMA 5–15 (110V) plugs. This lets you charge almost anywhere. A cable that's 25 feet long is also useful. It helps you connect from different spots easily.
Portability and Compact Design
Portable chargers should be easy to carry. The best ones are small and lightweight, fitting in your trunk. Some are as tiny as a bag and include a case for carrying. These chargers are great for trips, emergencies, or daily use. Their small size makes them simple to set up and use anywhere.
Durability and Weather Resistance
Your charger should handle tough weather. Rain, snow, or heat shouldn't stop it from working. UL-certified chargers are tested for harsh conditions. They work well outdoors, whether you're camping or charging at home. This makes them reliable in any situation.
Cost and Affordability
Price matters when choosing a charger. There are options for every budget. Don't pick a cheap one that lacks quality. Find a charger with good features like speed, compatibility, and durability. Spending more now can save you problems later.
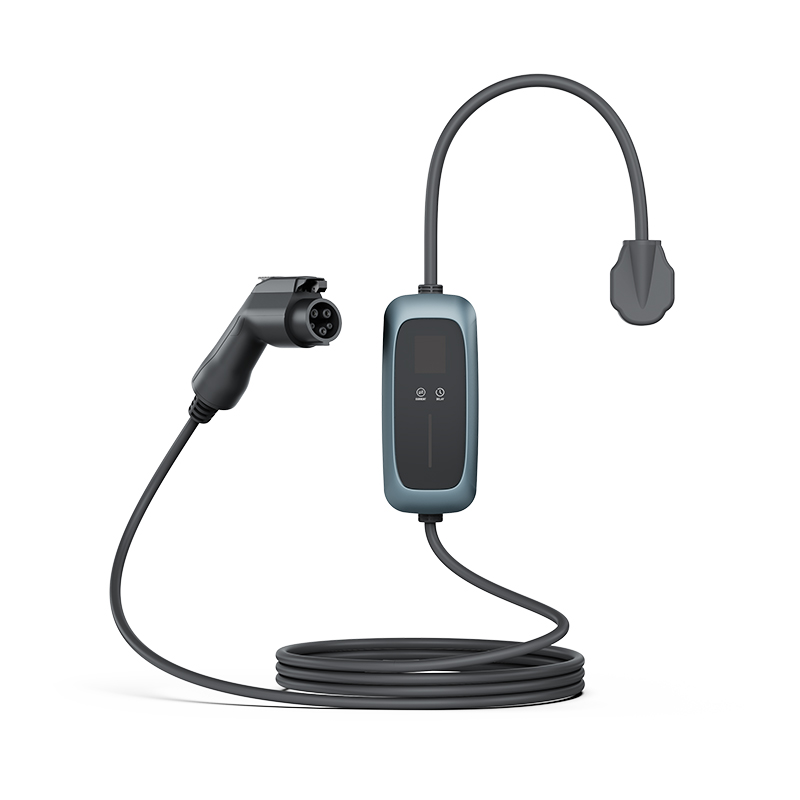
Top 10 Portable EV Chargers for Emergency and Travel
Tesla Mobile Connector
If you own a Tesla, this charger is essential. It’s small, simple to use, and works with 120V or 240V outlets. You can charge at home or while traveling. It’s dependable, especially in emergencies. Though made for Tesla cars, adapters let it work with other EVs. Its lightweight build makes it easy to carry for trips.
Grizzl-E Mini Connect 40A
The Grizzl-E Mini Connect 40A is powerful and compact. It provides Level 2 charging, adding up to 30 miles per hour. Its weatherproof design is great for outdoor use, like camping or storms. Built tough, it handles rough conditions well. If you want a durable and fast charger, this one is excellent.
EVDANCE Flux Portable EV Charger 40A
The EVDANCE Flux Charger has smart features like an LCD screen. It shows charging status, voltage, and temperature. It works with most EVs and charges quickly. The 25-foot cable lets you charge from far away, perfect for trips. Its sturdy design ensures it lasts through daily use.
AIMILER Level 2 EV Charger 32A
The AIMILER Charger is made for ease. It’s light, portable, and quick to set up. With 7.2 kW speed, it can fully charge overnight. Safety features like overcurrent protection keep you safe. It’s affordable and reliable, making it a good budget choice.
J+ Booster 2
The J+ Booster 2 is small but strong. It fits in your trunk and handles bad weather. It charges fast and works with many EVs. Smart features adjust power for safe charging. This charger is both flexible and dependable.
Juice Booster 2
The Juice Booster 2 is a high-end option for great performance. It’s built for home or travel and handles tough weather. It supports many plug types, so it works worldwide. Its fast charging and durability make it ideal for frequent travelers. Though pricey, its quality is worth it.
Emporia EV Charger
The Emporia Charger is perfect for tech lovers. It has an app to control charging remotely. You can track energy use and set charging times. It even works with solar panels. Its sleek look and smart features make it stand out.
Best for Solar Charging Integration
The Splitvolt Level 2 Charger is great for solar energy users. It works well with solar panels, letting you charge cleanly. It’s light, easy to install, and charges quickly. This charger helps you stay eco-friendly and ready for emergencies.
Best for Easy Installation
The Lectron Charger is super easy to set up. Just plug it in and start charging. It works with most EVs and performs reliably. Its small size makes it portable, and it’s affordable for many users.
Best Overall Value
The BougeRV Level 2 Charger offers great value. It’s affordable but packed with features like fast charging and durability. It works with many EVs and has safety features like overheat protection. Its long cable and weatherproof design make it useful for home or travel.
Pro Tip: When picking a portable EV charger, think about speed, compatibility, and durability. Smart features can make long trips much easier.
Buyer’s Guide to Emergency Portable EV Chargers
Understanding Charging Levels (Level 1 vs. Level 2)
It’s important to know the difference between Level 1 and Level 2 chargers. Level 1 chargers use regular 120 V outlets. They are slower and take 40-50 hours to fully charge a BEV. For a PHEV, they need about 5-6 hours. Level 2 chargers use 240 V outlets and are much faster. They can charge a BEV in 4-10 hours and a PHEV in 1-2 hours.
Here’s a simple comparison:
Charging Level
|
Voltage
|
Charging Time (BEVs)
|
Charging Time (PHEVs)
|
Percentage of Public Ports
|
Level 1
|
120 V
|
40-50 hours
|
5-6 hours
|
< 1%
|
Level 2
|
240 V
|
4-10 hours
|
1-2 hours
|
~80%
|
Most public chargers are Level 2, making them better for trips.
Safety Features to Prioritize
Safety is very important when picking a portable EV charger. Look for certifications like ANSI/UL 2594 or UL 2231-1. These show the charger meets safety standards. Features like overcurrent protection and temperature sensors help prevent problems. Weatherproof chargers are great for outdoor use.
Key safety features to look for:
-
Overcurrent and overvoltage protection.
-
Sensors to stop overheating.
-
Certifications like UL 2594 and UL 2231-2.
-
Weatherproof materials for outdoor charging.
Installation and Maintenance Tips
Setting up a portable EV charger is usually easy. Most are plug-and-play, so you just connect them to power. For Level 2 chargers, make sure you have a 240 V outlet. Take care of your charger by cleaning the connectors and checking cables for damage. Store it in a cool, dry place when not in use.
Warranty and Customer Support
A good warranty can save you money later. Look for at least a one-year warranty. Some brands offer longer warranties for extra peace of mind. Good customer support is also important. Pick a brand known for quick and helpful service. This way, you’ll get help if something breaks.
Pro Tip: Register your charger with the company to activate the warranty and get support easily.
Tips for Extending EV Range During Travel
Efficient Driving Techniques
Driving smoothly helps your EV go farther. Avoid quick starts or stops, as they waste energy. Keep a steady speed, especially on highways, to save battery power. Studies show driving habits affect energy use. For example, one driving cycle uses 12.9 kWh/100 km, while another uses 17.19 kWh/100 km. This shows that better driving can improve your EV's range and battery life.
Planning Charging Stops Strategically
Plan charging stops before long trips. Check for stations along your route. Pick places with many chargers to avoid waiting. Charging during the Constant Current (CC) phase adds range faster. Make sure stations are spaced within your EV's range. Good planning saves time and makes trips less stressful.
Using Regenerative Braking Effectively
Regenerative braking turns slowing down into battery power. It can boost your driving range by 25.7%. Up to 78% of braking energy can be reused. Factors like speed, road slope, and braking time affect how much energy is saved. Use this feature in traffic or downhill to make your EV more efficient.
Key Findings
|
Value
|
Range improvement
|
25.7%
|
Energy recovered during braking
|
78%
|
Factors affecting recovery
|
Weight, Speed, Road Slope, Braking Time
|
Reducing Energy Consumption from Accessories
Accessories like AC and heated seats use battery power. Use them less to save energy. Instead of AC, try using the fan or opening windows. Pre-condition your car while plugged in to save battery later. These small changes can add miles to your trip and make your EV last longer.
Pro Tip: Pair these tips with affordable portable EV chargers to stay ready for emergencies and extend your travel range.
Portable EV chargers are essential for trips and emergencies. They help reduce worries about running out of battery. Their light design makes them simple to carry anywhere. Level 1 chargers plug into regular outlets for easy charging. Buying a good charger keeps you prepared for any journey.